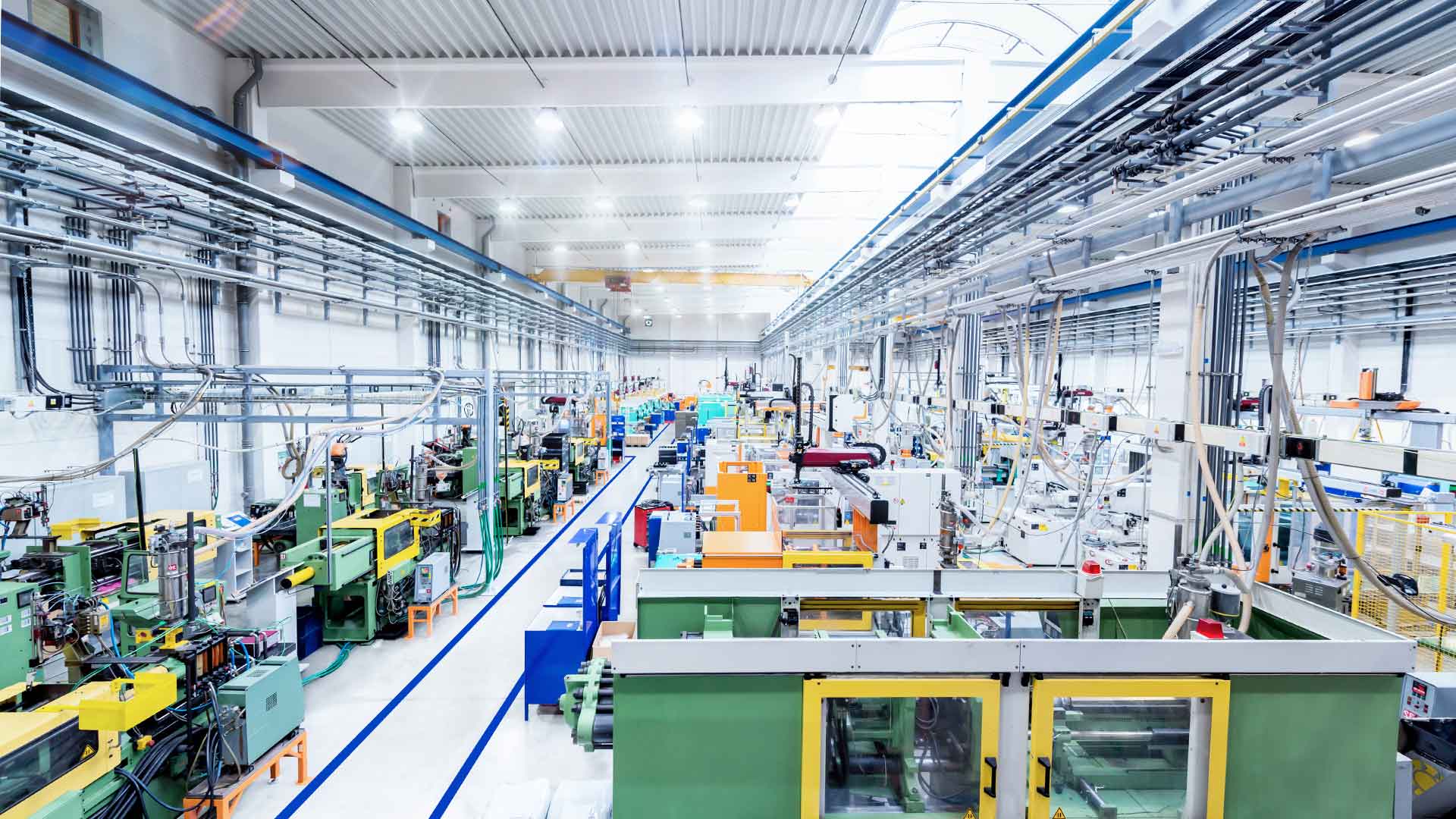
Industrial Equipment
Digitalize manufacturing to deliver made-to-order innovation.
The growing trends of the 4th Industrial Revolution - automation, IoT, artificial intelligence, big data analysis, networked communications, machine learning and cloud computing – mark a significant change in the way we work and how we engage with our customers.
These emerging technologies are providing advanced and disruptive Industrial Equipment solutions that support the creation, production and delivery of sophisticated and efficient machinery, equipment and components.
Serving the needs of all stakeholders across the Industrial Equipment value chain
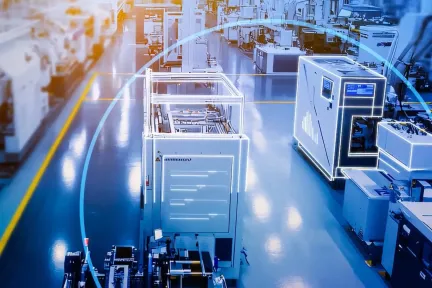
See how Dassault Systèmes’ industrial equipment solutions empower manufacturers to meet the digital demands of smart manufacturing — and stay ahead.
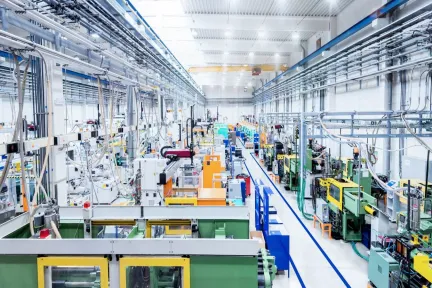
Single-function machines are being replaced by all-in-one equipment that covers the entire production process. To win more deals, manufacturers need to propose smarter and more flexible machines.
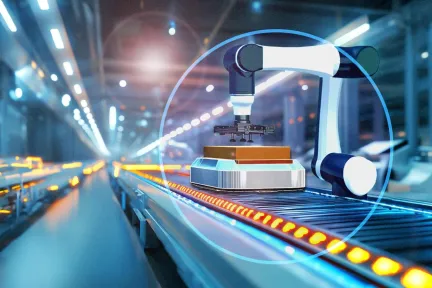
Driving Sustainable Innovation in Robotics, Machine Tools, and 3D Printing for Manufacturing Leadership.
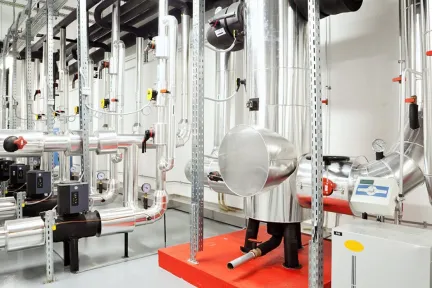
New technologies have transformed how power and fluidic equipment is designed by providing increased flexibility, accuracy, analytics and customization capabilities.
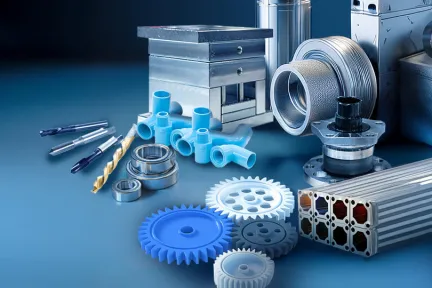
Empowering Fabricated Metal & Plastic Products Manufacturers to Drive Sustainable Innovation and Maximize Efficiency, Quality, and Profitability reaching Manufacturing Excellence.
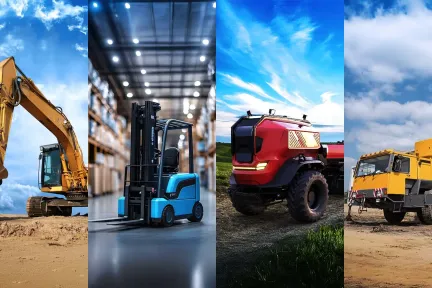
Discover robust, efficient and advanced heavy mobile equipment solutions tailored for the heavy mobile machinery market.
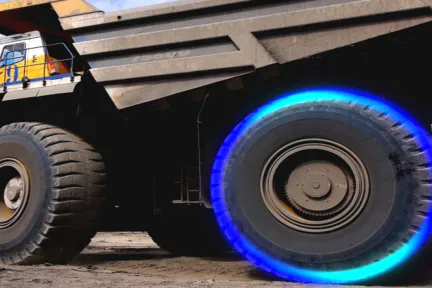
Rising fuel and raw material costs, fierce competition, and stringent safety and environmental regulations are just some of the challenges facing today’s tire manufacturers
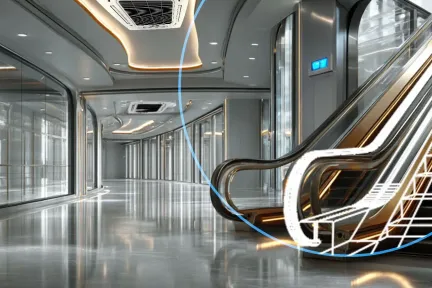
Reimagining elevators, escalators and HVAC systems starts in the virtual world. Here’s how the 3DEXPERIENCE® platform brings this vision to life.
Addressing the business challenges of the Industrial Equipment Industry
Emerging technologies are providing Industrial Equipment solutions that greatly revolutionize how manufacturers and suppliers of any size go-to-market.

Leverage flexible manufacturing to unlock lead time reduction and production scalability.
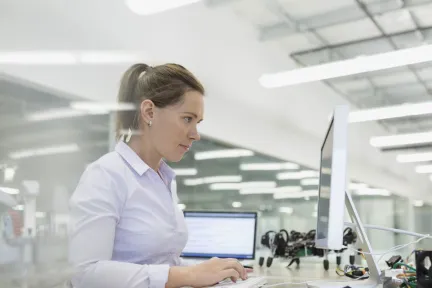
Accelerate machine versatility and performance from anywhere
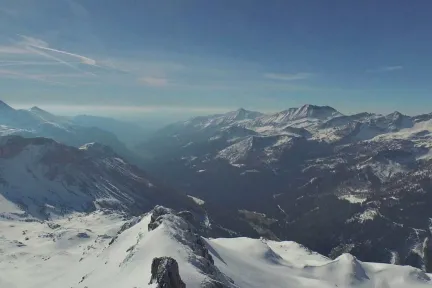
Ensure your business has the agility to meet the highly competitive pressure of customer demand.
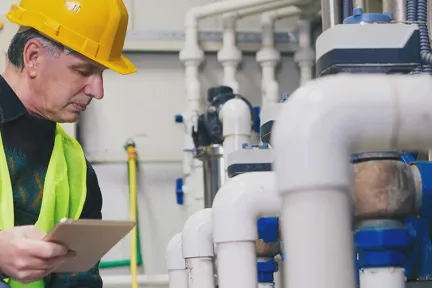
Keep operations running smoothly and expand after-sales revenue potential by including servicing needs at the beginning of the product development process
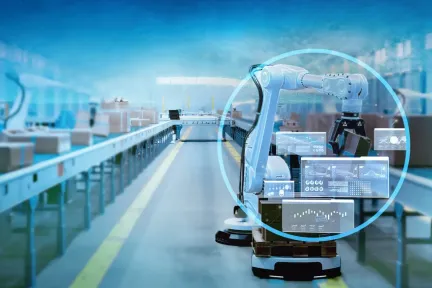
Discover how manufacturers can build operational and business resilience through risk mitigation, digital continuity and virtual twin technology.
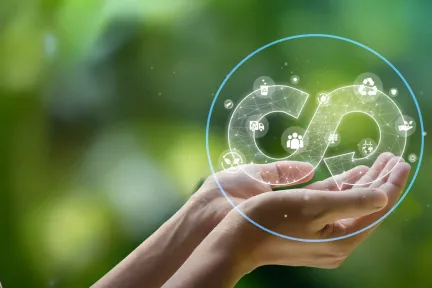
Unlock new sources of value: building sustainable and resilient industrial equipment in the circular economy.
In the Spotlight
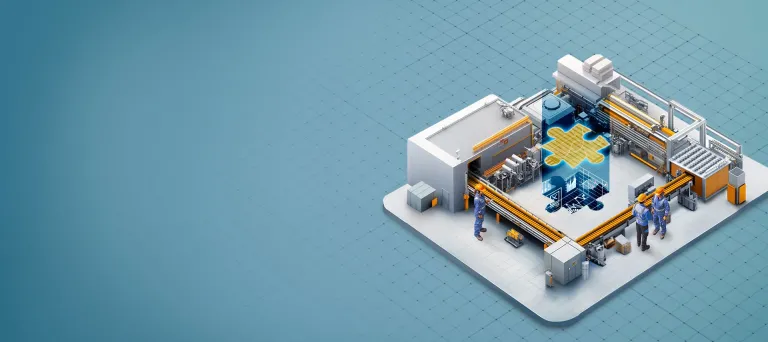
Unify operations, boost visibility and drive efficiency with DELMIA — your key to operational excellence.

Craft tire innovation excellence with the right integration and simulation strategy on the 3DEXPERIENCE® platform.
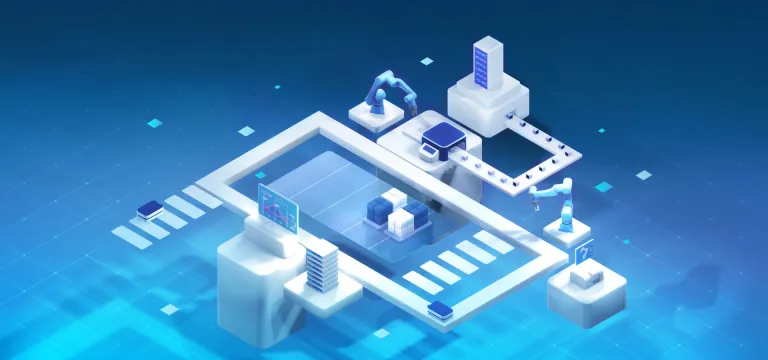
Develop, integrate, manage and maintain flexible production lines with autonomous mobile robots (AMRs).
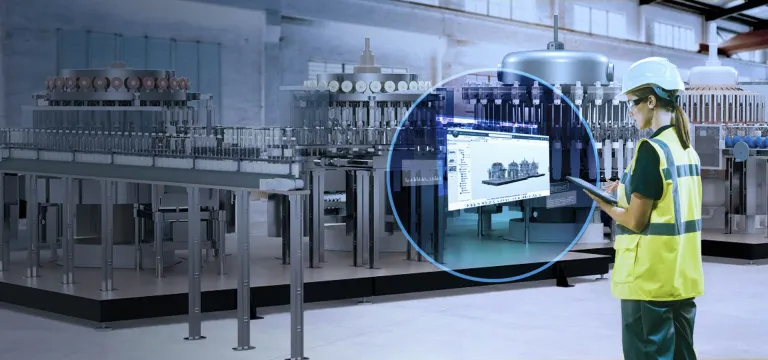
Virtual twins and advanced analytics drive performance optimization, operational efficiency, and superior customer service.
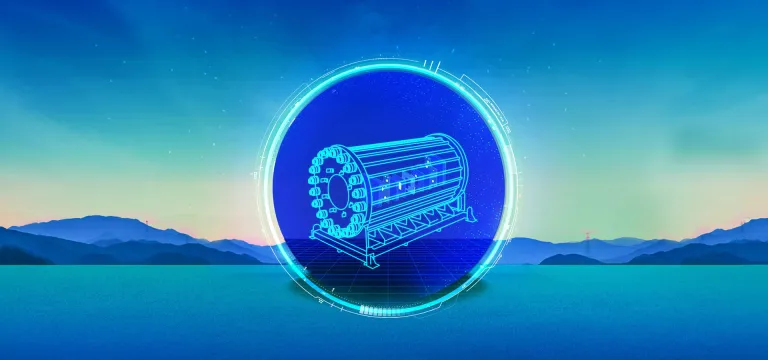
In a four-part series, experts reveal how the virtual twin delivers electrolyzers of the future to meet the demands of green hydrogen production.
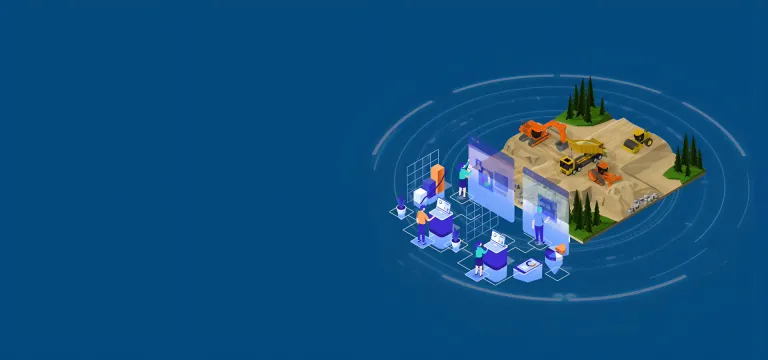
Model-Based Systems Engineering (MBSE) revolutionizes heavy mobile machinery and equipment development, enhancing collaboration, efficiency, and innovation
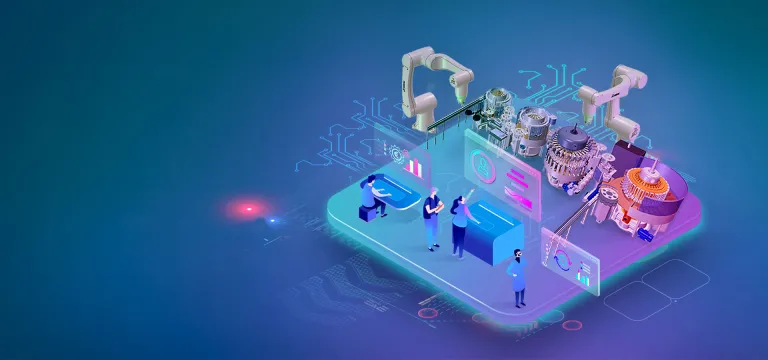
Leverage the 3DEXPERIENCE platform for greater field operations efficiency, after-sales services and success in the industrial equipment scene.
Explore our recent customer stories

Austrian machine builder automation.eXpress streamlines processes with Dassault Systèmes’ cloud-based Digital Equipment Continuity industry solution.
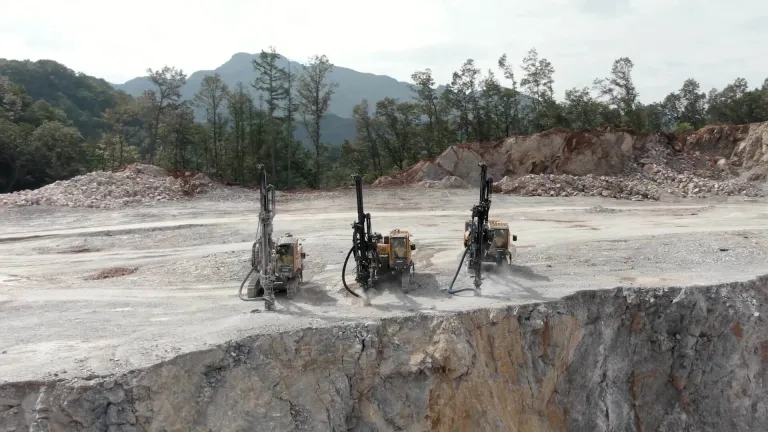
Soosan Cebotics is leveraging the 3DEXPERIENCE platform for end-to-end PLM, accelerating development of smarter, connected machinery.
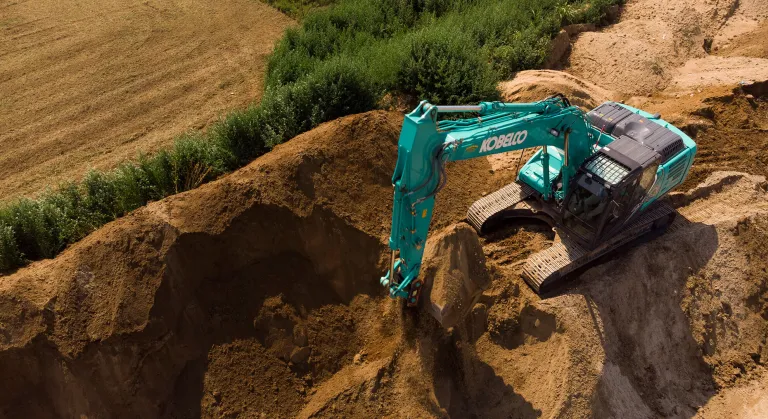
Kobelco Construction Machinery leverages the Single Source for Speed and Integrated Heavy Machinery solutions to optimize design processes and improve access to information across its organization.
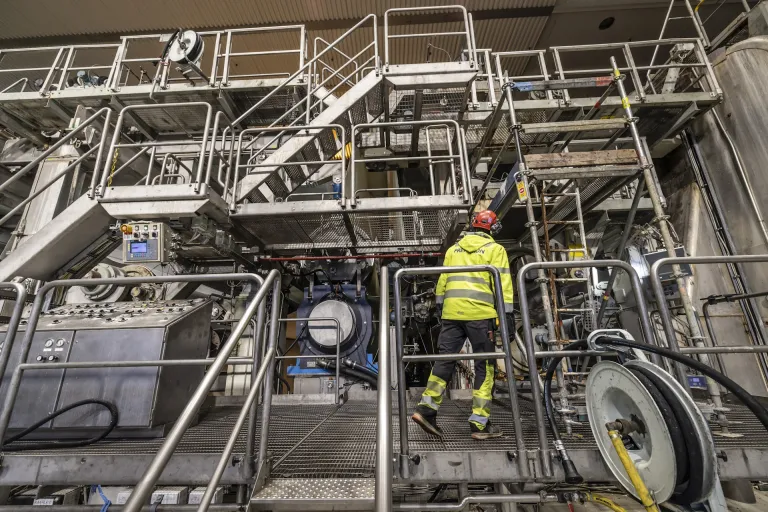
The Finnish company uses the Digital Equipment Continuity industry solution to design and manufacture steel structures and service platforms while improving data management and collaboration.
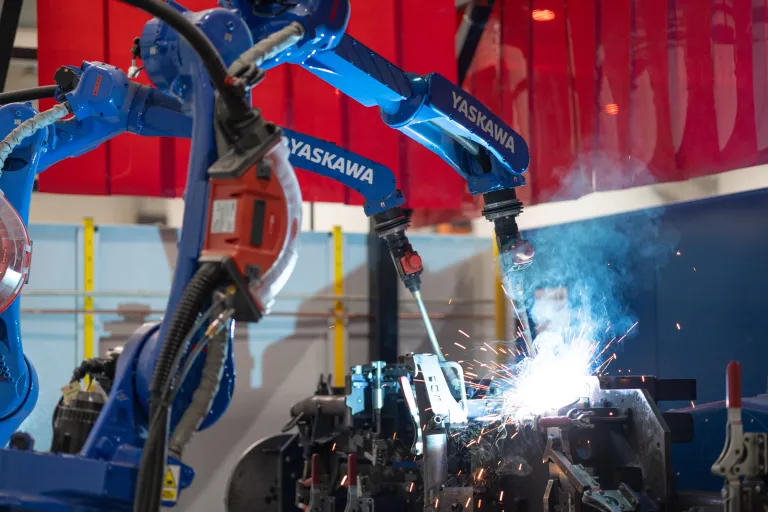
Polish Stelweld is shaping the future of metal fabrication with its latest welding techniques and adopted the 3DEXPERIENCE platform to refine its production processes. With the Digital Equipment Continuity industry solution experience, the company can create a seamless workflow and has the ability to simulate and virtually test product designs, helping them to meet customer demands faster while maintaining high quality standards.
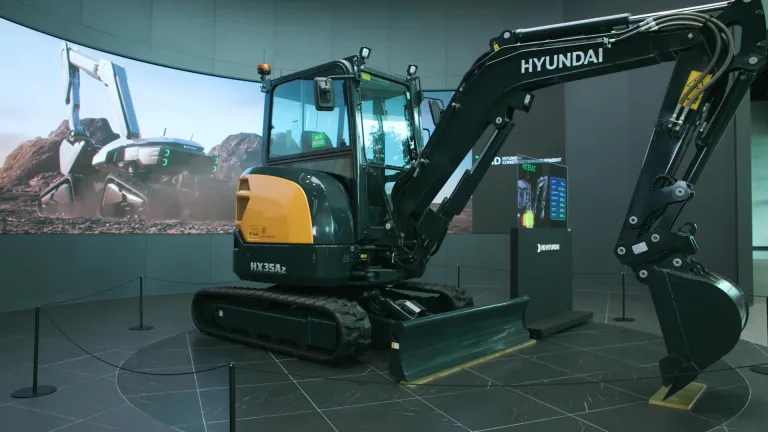
To foster greater synergy between its two subsidiaries, Korean construction machinery company HD Hyundai XiteSolution needed to create a common global product development management system to integrate their design, product lifecycle and bill of materials management capabilities.
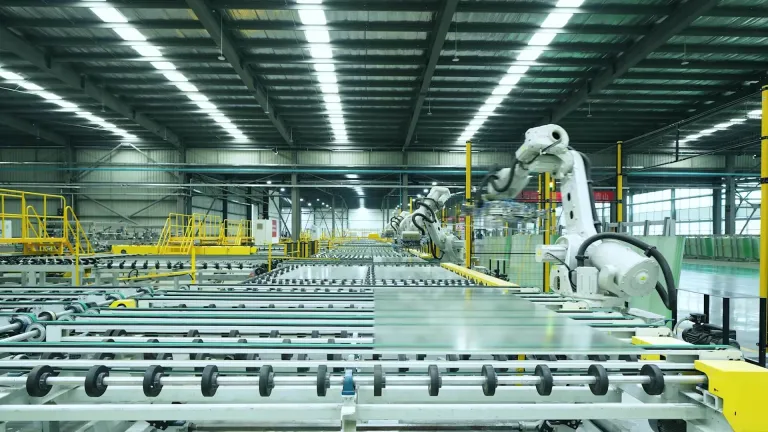
Shanghai-based robotic line builder CNBM Triumph Robotics adopted the 3DEXPERIENCE platform's Digital Equipment Continuity industry solution experience to streamline and standardize its way of working. With virtual commissioning, customers now experience the production lines through virtual twins, which support them with diagnostics, equipment upgrades and training.
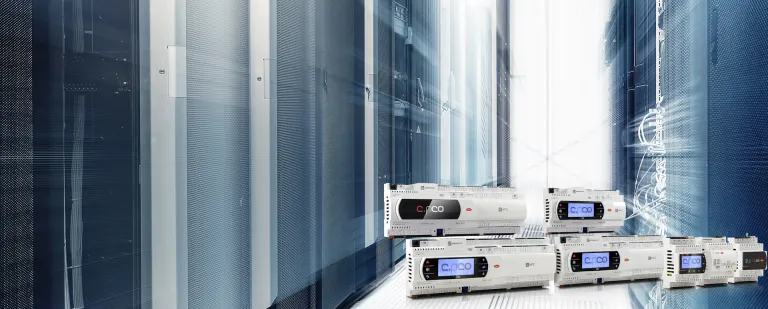
Italian company CAREL specializes in electronic control solutions for air conditioning, refrigeration and heating systems and uses the 3DEXPERIENCE platform on the cloud for its development processes. By adopting the Digital Equipment Continuity industry solution experience, CAREL is able to connect all disciplines and systems, which shortens configuration and production time, reduces errors and offers more customization options.
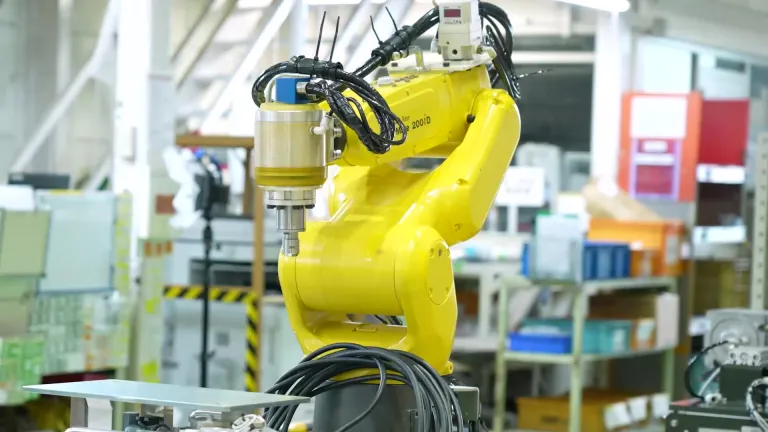
Japanese robotic assembly line builder Yutaka Electronics chose Dassault Systèmes’ 3DEXPERIENCE platform on the cloud and its industry solution experience Digital Equipment Continuity to ensure that the systems it has designed for its customers are operating correctly and efficiently before it begins physical commissioning.
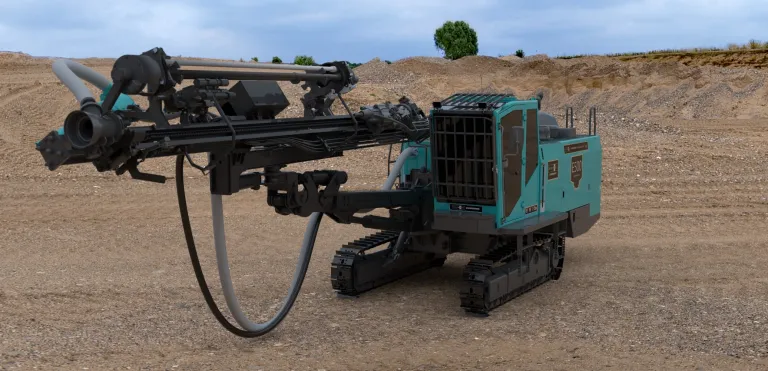
Korean heavy mobile equipment manufacturer Hyundai Everdigm serves the construction and civil engineering sectors with its fire trucks, concrete pump cars, hydraulic drills and more. The company migrated from its legacy PLM system to Dassault Systèmes’ 3DEXPERIENCE platform, using industry solution Digital Equipment Continuity to transform its product development, optimize its manufacturing operations and achieve a continuous data flow across the entire product lifecycle.
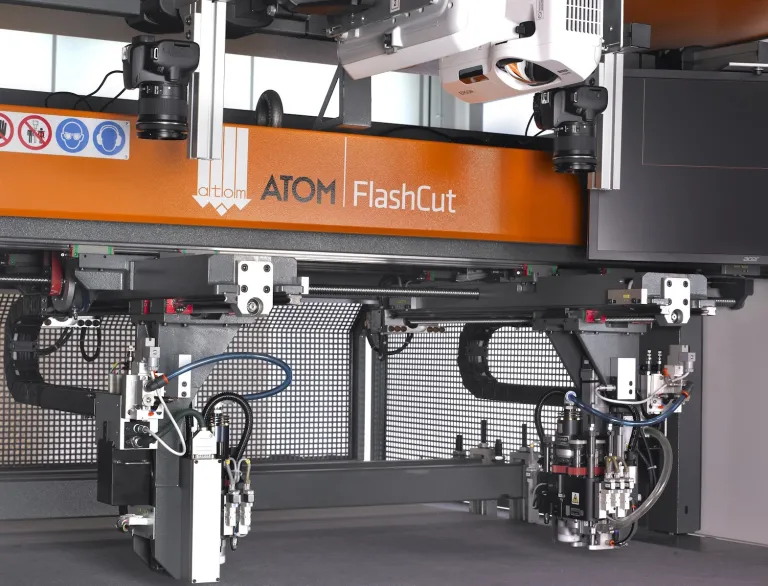
Italian cutting machine manufacturer ATOM CUTTING is a leading global provider of innovative cutting systems for a range of industries from fashion to aerospace and uses the 3DEXPERIENCE platform on the cloud for its product development processes. With the Digital Equipment Continuity industry solution experience, ATOM can centralize all product development data and bring together different disciplines within a single environment.
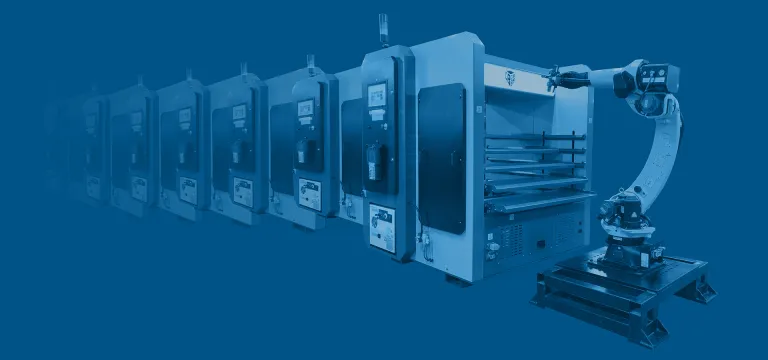
Struggling to manage the large and complex assembly data for its robotic automation systems, Tezmaksan Robot Technologies relies on Dassault Systèmes’ solution for its powerful design and data management capabilities. The Digital Equipment Continuity industry solution experience provides a centralized environment through which the engineers can work concurrently in real time, reducing duplicate data and improving efficiency.